In today’s fast-paced, technology-driven world, industries are constantly seeking ways to improve efficiency, reduce downtime, and enhance decision-making processes. One of the most innovative developments in industrial operations is the concept of the Digital Twin—a virtual replica of physical systems, processes, or assets. When combined with SCADA (Supervisory Control and Data Acquisition) systems, Digital Twins are transforming industries by offering real-time insights, predictive analytics, and streamlined operations.
What is SCADA and Digital Twin?
Before diving into the powerful combination of SCADA and Digital Twins, it's important to understand both concepts individually.
- SCADA is a control system architecture used to monitor and control industrial processes in real-time. It allows operators to remotely monitor equipment, collect data from sensors, and make decisions based on live information. SCADA systems are commonly used in industries such as manufacturing, energy, water treatment, and transportation.
- Digital Twin is a virtual representation of a physical object, system, or process, which is updated in real-time based on data from sensors and other input sources. This digital replica can be used for simulation, analysis, and optimization, helping industries improve performance, predict issues, and enhance product design.
Now, imagine the power of integrating these two technologies: SCADA provides the data collection and real-time monitoring capabilities, while the Digital Twin acts as a virtual representation that simulates, analyzes, and predicts outcomes based on that data.
The Role of SCADA in Digital Twin Technology
SCADA systems serve as the data backbone for Digital Twin applications. By continuously collecting real-time data from sensors embedded in physical assets or processes, SCADA creates a live stream of information. This data is then used to update and optimize the Digital Twin, providing a dynamic virtual model that mirrors the physical world. Here’s how SCADA and Digital Twins work together to drive industrial transformation:
- Real-Time Monitoring & Control: SCADA systems are designed to monitor industrial assets in real-time, capturing operational data such as temperature, pressure, humidity, energy consumption, and equipment status. When this data is fed into a Digital Twin, industries can instantly observe the condition and performance of assets in a digital environment, providing real-time visibility that was previously unattainable.
- Predictive Maintenance & Optimization: One of the most powerful benefits of SCADA-enabled Digital Twins is the ability to perform predictive maintenance. By analyzing historical data from SCADA systems and continuously monitoring the performance of equipment, Digital Twins can predict potential failures before they happen. This allows industries to perform maintenance proactively, reducing downtime, lowering maintenance costs, and improving asset longevity.
- Enhanced Decision-Making: With SCADA feeding real-time data into Digital Twins, industries can simulate various scenarios, test operational strategies, and predict the outcomes of different decisions. This helps management teams make informed, data-driven decisions that optimize operations, minimize risks, and improve overall efficiency. The ability to “what-if” test scenarios in a virtual environment without risking physical assets is a game changer for industries.
- Improved Product Design & Development: In manufacturing, SCADA-driven Digital Twins can be used to simulate the performance of products before they are built. Engineers can test various configurations, materials, and processes in a virtual space to identify design flaws, optimize production cycles, and enhance product quality. This is especially useful in industries like automotive, aerospace, and electronics, where design accuracy and production efficiency are crucial.
- Energy Efficiency and Sustainability: SCADA systems track energy consumption and operational data, which is critical for optimizing processes for energy efficiency. By integrating this data with Digital Twins, industries can model the energy usage of their systems and simulate improvements. This can result in reduced energy consumption, lower costs, and a smaller environmental footprint—benefits that are vital in today’s sustainability-driven world.
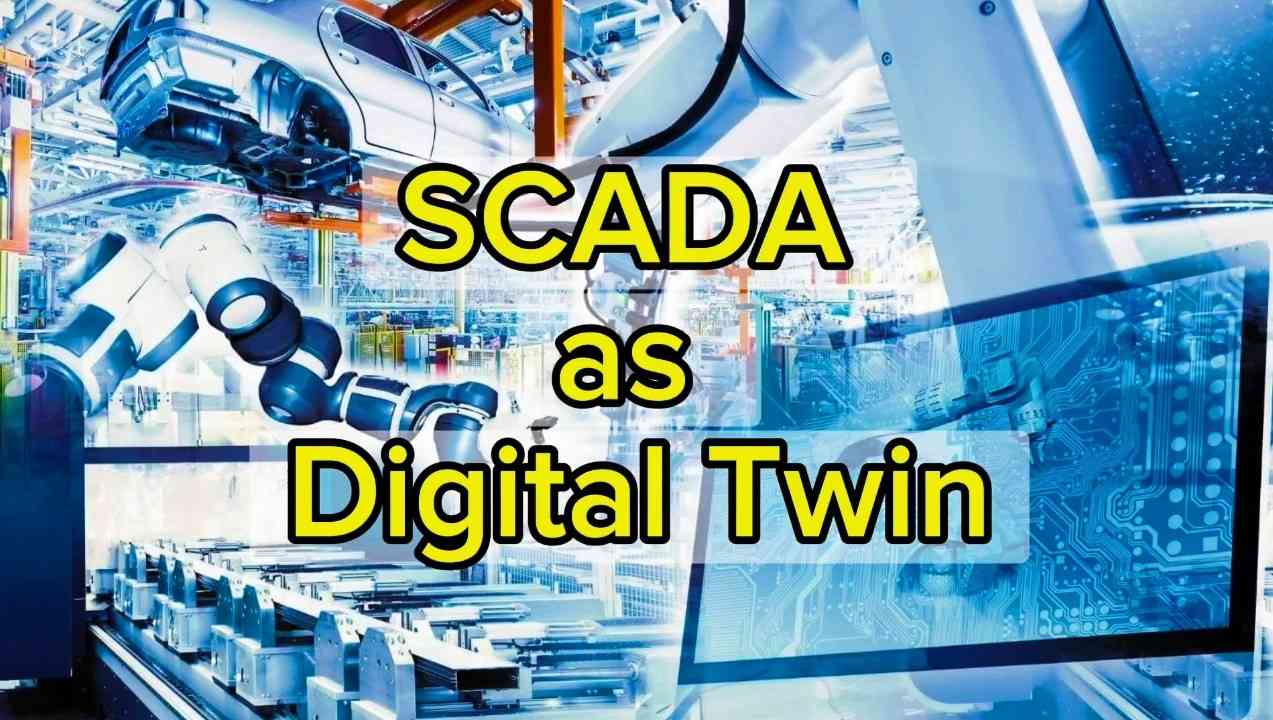
Applications of SCADA as a Digital Twin Across Industries
The integration of SCADA with Digital Twins is gaining traction across a wide range of industries. Here are some key examples of how this combination is transforming operations:
- Manufacturing: In manufacturing plants, SCADA systems track machinery performance, production speed, and operational conditions. By creating a Digital Twin, manufacturers can simulate production lines, test new configurations, and optimize workflows without disrupting actual operations.
- Energy: Power plants and utilities use SCADA systems to monitor and control energy production and distribution. Integrating SCADA with Digital Twins enables power grids to simulate different energy loads, forecast demand, and optimize distribution. It also allows for improved maintenance scheduling and better grid management.
- Oil & Gas: SCADA systems in the oil and gas industry monitor remote operations such as drilling, pipelines, and refineries. By feeding this data into a Digital Twin, companies can simulate different drilling scenarios, monitor pipeline integrity, and optimize production processes, reducing the risk of accidents and increasing productivity.
- Transportation & Infrastructure: Transportation networks, such as railways, airports, and roadways, use SCADA to track vehicles, traffic flow, and infrastructure health. When paired with Digital Twins, SCADA data can be used to optimize routes, improve traffic management, and predict infrastructure failures, enhancing the safety and efficiency of transportation systems.
- Water Management: SCADA is extensively used in water treatment plants to monitor water quality, pump performance, and flow rates. By leveraging Digital Twins, water utilities can simulate different scenarios, forecast demand, and optimize water distribution systems, ensuring more efficient resource use and better service for communities.
The Future of SCADA and Digital Twins
As industries continue to embrace Industry 4.0 technologies, the integration of SCADA and Digital Twin technology will only grow in importance. Advancements in artificial intelligence, machine learning, and cloud computing are making it easier to build and scale these systems, further enhancing the potential of SCADA as a Digital Twin for industries. In the future, the combination of SCADA and Digital Twins will allow for greater automation, deeper insights into operations, and more intelligent decision-making. Industries will not only be able to optimize their current processes but also create entirely new business models based on data-driven innovation.
Conclusion
The integration of SCADA and Digital Twin technology is a game changer for industries looking to optimize operations, reduce downtime, and improve overall efficiency. By combining real-time monitoring with predictive analytics and simulation, companies can achieve unprecedented levels of performance and agility. As this technology continues to evolve, SCADA-driven Digital Twins will be at the forefront of the industrial transformation, paving the way for smarter, more sustainable operations across the globe.